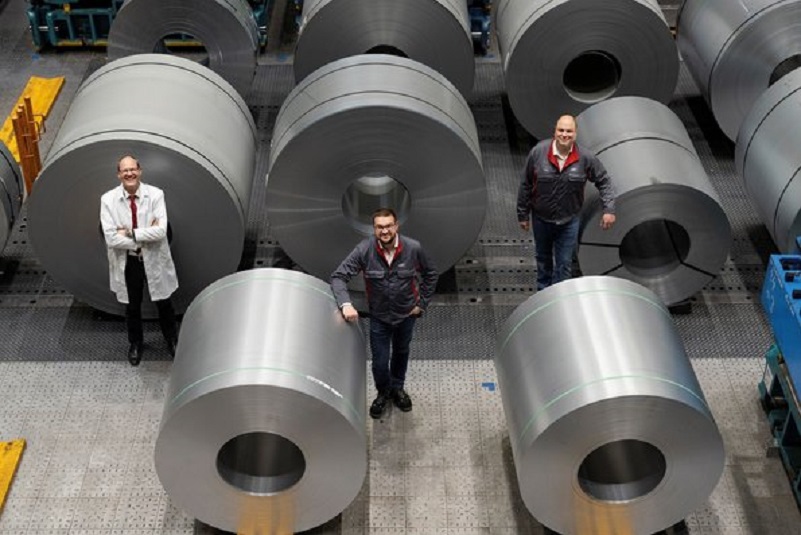
New basic lubrication for steel coils in the press shop saves 40 metric tonnes of oil every year
Volkswagen Group set to roll out this Audi-initiated product development
Board Member for Production, Peter KĂśssler: âEvery contribution to increasing resource efficiency helpsâ
Audi production processes are set to become even more sustainable in the future: With the start of production of the Audi Q6 e-tron, Audi is introducing the second-generation steel coil lubrication Prelube II. This new product will help to significantly reduce the amount of lubricant required for protecting against corrosion and machining the metal sheets in the press shop. The idea originated from Audi employees in the press shop in Ingolstadt â and has already caught on at the Volkswagen Group.
With the conventional lubrication Prelube I, one gram of oil is applied over every square meter of sheet steel. With the new lubrication class Prelube II, however, just 0.7 grams of oil are required for every square meter â and with almost identical processing parameters.
The new oil class creates a protective film on the surface of a metal sheet that is thicker and does not run off. For the reinforcement frame of the roof of the Audi A4, for example, just 2.7 grams of Prelube II are needed instead of the usual 3.9 grams of conventional oil. Extrapolated to all steel components that Audi machines at its production locations in Europe and Mexico, this offers incredible savings potential of around 40 metric tonnes of oil every year compared with the same period in 2018.
âAt Audi, weâre always thinking about how to make our process steps in production and logistics more sustainable over the long term. Every contribution to increasing resource efficiency and achieving the ambitious targets behind our Audi environmental campaign Mission:Zero helps,â says Peter KĂśssler, Board Member for Production and Logistics at AUDI AG.
With the start of production of the Audi Q6 e-tron in Ingolstadt, the Prelube II oil class has been set as the new standard for steel coil lubrication. Audi will then look at the other model series that are currently in production, trial the new product for each and every component and then switch the production process to Prelube II.
The idea has caught on: âWe have managed to persuade our steel suppliers to switch to Prelube II â a technically challenging process but one that will help to conserve resources over the long term,â says Dr. Ingo Faass from operations management at the press shop in Ingolstadt.
âThe Volkswagen Group, too, has eagerly adopted our initiative and is planning to introduce the new oil class in Europe as the standard. This will increase the savings potential even more.â The VDA has also been talking about the optimized lubrication, with other manufacturers likely to start using Prelube II in the coming years.
Even lubrication and lower consumption
The Prelube protective film applied by the steel producers prevents corrosion and ensures that the process of forming the flat sheets into individual pieces in the Audi press shop quite literally runs like a well-oiled machine. The first-generation Prelube oils, however, always suffered from the problem that oil would escape from the sheet steel rolls and contaminate the storage areas in the press shop. On top of this, the thin and sometimes unevenly applied lubrication would lead to problems during subsequent machining of the steel panels. A better solution was needed.
To fix these problems, employees from different departments â technology development, the tool and body shop and purchasing â collaborated very closely to develop and approve Prelube II. Compared with Prelube I, this second-generation product offers another key benefit: Since the protective lubrication needs to be washed off thoroughly before the body can be painted, a thinner film of oil on the steel coils is much more environmentally friendly.
âIn future degreasing processes, we will be able to significantly reduce the amount of cleaner that we use and, in particular, its surfactant content,â says Martin Michallek from Paint Shop Production Planning in Ingolstadt.
Audiâs Mission:Zero campaign â step by step toward sustainable production
Audi bundles all measures for reducing the ecological footprint at its production locations worldwide in Production and Logistics in the Mission:Zero environmental program. The focus is on decarbonization, water use, resource efficiency and biodiversity. One central goal of Mission:Zero is to ensure that all Audi locations are carbon-neutral by 2025.